工場の電気代削減!9つの方法|電力会社乗り換えも
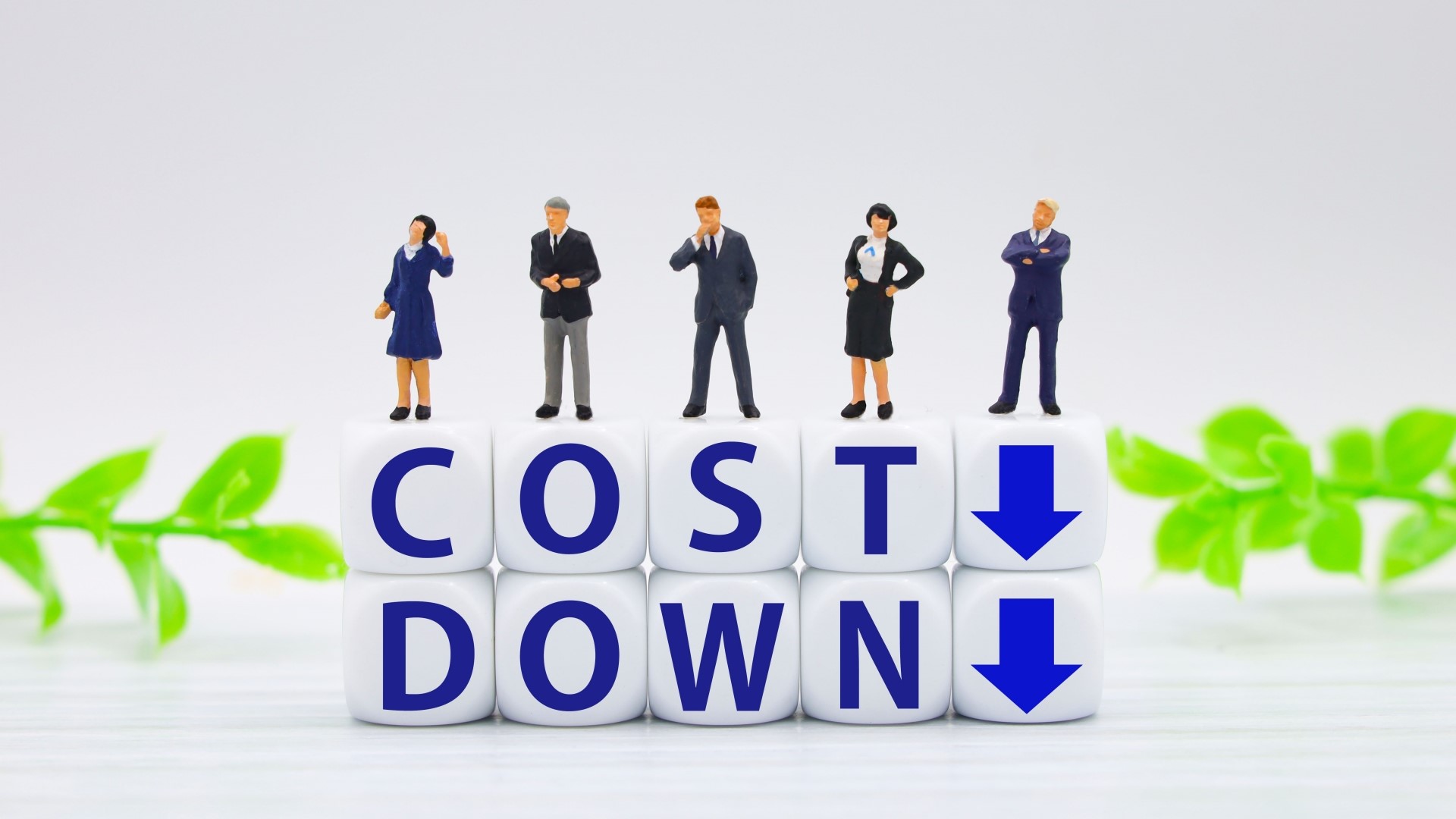
工場における電気代の削減は、企業の収益性と環境負荷の両面で重要な課題となっています。本記事では、すぐに実践できる9つの具体的な削減方法から、補助金の活用まで、包括的な対策をご紹介します。電力会社の切り替えだけでなく、設備の最適化や従業員の意識改革など、多角的なアプローチで確実な削減効果を実現しましょう。
なぜ工場の電気代削減が重要なのか?
製造業において、電気代は経営を圧迫する大きな要因となっています。近年の電力料金の上昇により、多くの工場では年間の電気代が運営費用の20~30%を占めるまでに増加しています。電気代の削減は、単なるコスト削減以上の意味を持っているのです。
具体的には、電気代の削減によって得られる利点は以下の通りです。
● 製品の原価低減による競争力の向上
● 環境負荷の低減によるSDGsへの貢献
● 省エネ補助金の獲得機会の増加
たとえば、月間電気代が100万円の工場で20%の削減に成功した場合、年間240万円のコスト削減が実現できます。この削減分を設備投資や従業員の待遇改善に回すことで、さらなる企業価値の向上につながるのです。
工場の電気代が高い原因とは?
工場の電気代が高騰する主な要因は、設備の非効率な運用と電力契約の最適化不足にあります。多くの工場では、古い設備をそのまま使い続けていたり、ピーク時の電力使用量を適切に管理できていなかったりすることで、必要以上の電気代を支払っている状況にあります。
特に注意が必要なのは以下のような状況です。
● 設備の稼働時間と電力単価の高い時間帯が重なっている
● 老朽化した設備による電力効率の低下
具体的な例として、ある金属加工工場では、大型プレス機を電力単価の高い日中に集中して稼働させていたため、月間の電気代が近隣の同業他社と比べて30%も高くなっていました。この工場が稼働時間の見直しを行った結果、電気代を年間で約400万円削減することに成功しています。
今すぐできる!工場の電気代削減9つの方法
① 電力会社の見直し・切り替え
電力自由化により、工場でも電力会社を自由に選択できるようになりました。契約の見直しによって、年間の電気代を5~15%程度削減できる可能性があります。
まずは現在の電力使用状況を詳細に分析し、最適な料金プランを提供している電力会社を選定することが重要です。例えば、大規模な工場であれば、特別高圧電力を供給できる電力会社との契約が有利になる場合があります。
また、複数の電力会社から見積もりを取得し、以下の点を比較検討することをお勧めします。
● 基本料金と従量料金の単価
● 契約期間と解約条件
● 電力の安定供給体制
② 照明設備のLED化
工場の照明をLEDに切り替えることで、照明にかかる電気代を最大70%削減することができます。初期投資は必要ですが、一般的に2~3年で投資回収が可能です。
③ 空調設備の最適化
空調設備は工場の電力消費の中でも大きな割合を占めており、適切な管理と運用によって大幅な電気代削減が可能です。特に重要なのは、温度設定の適正化と運転時間の最適化です。
具体的な対策として、以下のような取り組みが効果的です。
● 季節や時間帯に応じた温度設定の自動制御
● 断熱材の施工による空調効率の向上
例えば、ある食品工場では、製造エリアの空調設定温度を1℃緩和し、扉の開閉時間を管理することで、空調にかかる電気代を年間15%削減することに成功しました。さらに、天井への断熱材の追加施工により、夏季の空調負荷を20%低減させています。
④ 生産設備の効率化
生産設備は工場の電力消費の中核を担っており、その効率化は電気代削減に大きな効果をもたらします。具体的には、設備の稼働スケジュール最適化とメンテナンス体制の強化が重要です。
例えば、大規模な機械加工工場では、以下のような取り組みにより、年間の電気代を25%削減することに成功しています。
● 生産計画の見直しによる設備稼働率の向上
● 予防保全の実施による設備効率の維持
特に注目すべきは、IoTセンサーを活用した設備監視システムの導入です。これにより、設備の電力消費状況をリアルタイムで把握し、効率的な運用が可能となります。
⑤ 動力設備の見直し
モーターやポンプなどの動力設備は、工場全体の電力消費の40~60%を占めることもあり、その最適化は電気代削減の重要なポイントとなります。
効果的な対策として、以下が挙げられます。
● インバータ制御の導入による電力消費の最適化
● 高効率モーターへの更新
具体的な成功事例として、化学工場での取り組みがあります。この工場では、主要なポンプ設備にインバータを導入することで、動力設備の電力消費を30%削減することに成功しました。初期投資額は1,500万円でしたが、年間の電気代削減額が600万円となり、2.5年で投資回収を達成しています。
⑥ ピークカット・ピークシフト
電力需要のピーク時間帯を避けることで、基本料金の削減が可能です。これには、生産計画の見直しと蓄電システムの活用が効果的です。
たとえば、大手自動車部品工場では、以下のような取り組みを実施しています。
● 電力需要の高い工程を夜間にシフト
● 蓄電池システムの導入によるピークカット
この取り組みにより、契約電力を15%削減し、年間の基本料金を約1,000万円削減することに成功しました。
⑦ エネルギー管理システム(EMS)の導入
EMSの導入により、工場全体のエネルギー使用状況を可視化し、効率的な運用が可能となります。リアルタイムでの電力使用量の把握とAI活用による最適制御が、電気代削減の鍵となります。
具体的な導入効果として、以下が期待できます。
● デマンド監視による契約電力の超過防止
● 設備ごとの電力使用量分析による無駄の特定
ある電子部品工場では、EMSの導入により年間の電気代を18%削減することに成功しています。投資額3,000万円に対し、年間削減額が900万円となり、約3.3年での投資回収を実現しました。
⑧ 太陽光発電の導入
工場の屋根や未利用地を活用した太陽光発電システムの導入は、電気代削減の有効な手段です。特に、FIT制度や自家消費型の太陽光発電の活用により、大きな削減効果が期待できます。
導入を検討する際のポイントは以下の通りです。
● 設置場所の日照条件と構造強度の確認
● 系統連系の可能性と費用の検討
例えば、某製造業の工場では、2,000㎡の屋根に太陽光パネルを設置し、年間使用電力の15%を賄うことで、電気代を年間約1,200万円削減することに成功しています。
⑨ 従業員の意識改革と啓蒙活動
電気代削減の取り組みを成功させるためには、従業員一人一人の意識改革が不可欠です。具体的な施策として、以下のような取り組みが効果的です。
● 省エネ研修の定期的な実施
● 節電目標の設定と達成状況の共有
ある工場では、従業員参加型の省エネ活動を展開し、小さな改善の積み重ねにより、年間の電気代を8%削減することに成功しています。
電気代削減効果を高めるポイント
電気代削減の効果を最大化するためには、個々の対策を単独で実施するのではなく、総合的なアプローチが必要です。特に重要なのは、PDCAサイクルの確立と投資効果の検証です。
効果的な推進のためのポイントは以下の通りです。
● 現状分析に基づく優先順位の設定
● 定期的な効果測定と改善策の実施
例えば、包装資材製造の工場では、複数の対策を組み合わせることで、年間の電気代を35%削減することに成功しています。この工場では、まず使用状況の詳細な分析を行い、投資対効果の高い施策から順次実施していきました。
補助金・助成金活用で更なるコスト削減
省エネ設備への投資には、様々な補助金や助成金を活用することができます。主な制度として、以下のようなものがあります。
● 省エネ補助金(最大1億円)
● 民間金融機関による環境融資
具体的な活用事例として、ある中小製造業では、LED照明とEMSの導入に際して補助金を活用し、実質的な投資額を当初の計画から45%削減することに成功しています。
【まとめ】電気代削減で工場経営を安定化
工場の電気代削減は、単なるコスト削減だけでなく、企業の競争力強化と環境負荷低減に直結する重要な取り組みです。本記事で紹介した9つの方法は、いずれも実績のある効果的な対策です。
特に重要なポイントを整理すると。
● 現状分析に基づく適切な対策の選択
● 複数の施策の組み合わせによる相乗効果の追求
まずは自社の状況に合わせて、実施可能な対策から順次取り組んでいくことをお勧めします。電気代削減の取り組みは、工場経営の安定化と持続可能な成長への重要な一歩となるはずです。